Unleashing Value: The Power of Value Engineering in Product Design
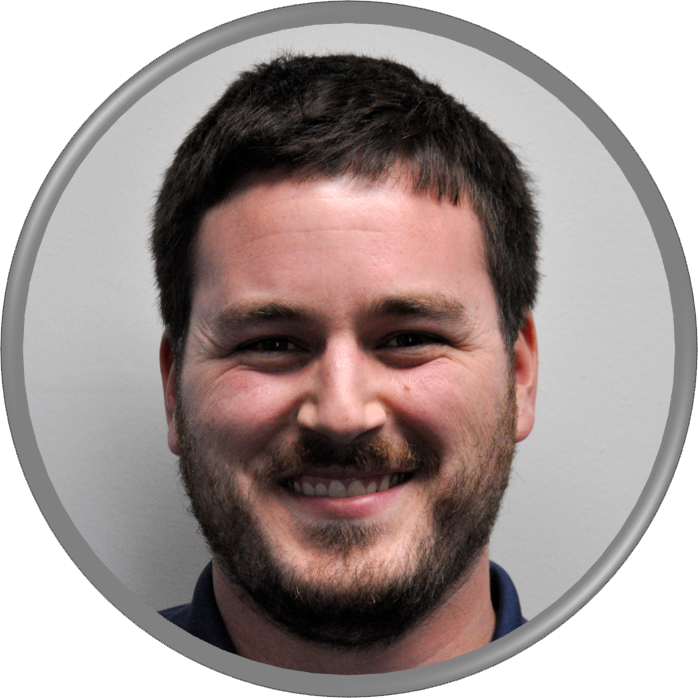
Written by Don Rysdyk
During World War II, General Electric (GE) faced significant challenges—shortages of labor, raw materials, and essential components. As GE engineers searched for alternatives to replace these scarce resources, they made an unexpected discovery: the substitutes resolved supply issues and resulted in cost savings and product enhancements. This breakthrough laid the groundwork for a systematic approach known as "value analysis," which eventually evolved into what we now call value engineering.
What is Value Engineering?
Value engineering is a systematic method focused on improving the "value" of products and services by analyzing their function and cost.
The Value Formula
∗∗Value=Function/Cost∗∗
Breakdown of the Formula:
- Function: The specific tasks or actions a product performs.
- Cost: All associated material and time expenses, including manufacturing and testing.
- Value: Achieving desired functionality in the most cost-effective manner that meets user expectations.
While interpretations may vary, the core objective remains the same: enhance product value by optimizing function and decreasing cost.
Decreasing Cost While Maintaining Functionality
There are two main approaches to value engineering. The first involves cost reduction without sacrificing functionality, which is often pursued by OEMs to boost profit margins. Key areas include:
1. Reducing Purchase Prices
- Explore New Suppliers: Switching suppliers and improving fabrication processes can save costs.
- Analyze High-Cost Components: Focus on optimizing the most expensive parts for maximum savings.
2. Reducing or Combining Components
- Component Consolidation: Combining parts or removing unnecessary components aligns with Design for Manufacturability (DfM) principles, emphasizing simplicity and cost savings.
3. Supplier Consolidation
- Increase Volume with Fewer Suppliers: In-house versus outsourced production decisions and strategic supplier relationships can drive cost efficiency.
4. Assembly Process Improvements
- Optimize Assembly Steps: Evaluate assembly fixtures and procedures for efficiency gains. Internal Kaizen events or third-party reviews often uncover valuable improvement opportunities.
5. Testing Process Enhancements
- Streamline Testing: Efficiently balance risk and cost by refining testing procedures, crucial for capital equipment manufacturing.
The Turnkey Assembly Supplier Advantage
OEMs can maximize value engineering benefits by consolidating higher-level assembly sourcing with a single supplier. Working closely with a supplier who understands product assembly leads to more comprehensive assessments and improvements. Additionally, a single-source supplier can leverage their existing relationships and purchasing power for lower component costs while reducing the OEMs overhead by managing a single SKU versus the full bill of materials.
Increasing Functionality While Maintaining Cost
Beyond cost reduction, value engineering can also focus on enhancing functionality. Adding new features without increasing costs can improve a product’s value proposition, setting it apart from competitors.
Value engineering is more than a strategy; it's a pathway to innovation and sustainable profitability. By refining processes and rethinking traditional manufacturing approaches, OEMs can continue delivering quality products that meet customer needs at an optimal cost.
Explore how GMI Solutions can partner with you to optimize value through strategic supply chain management and innovative manufacturing practices.