Supply Chain Outlook: Turbulence For 2021
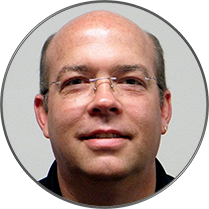
Written by Hans Dittmar
Good news, bad news: faster-than-expected increases in demand causing supply chain issues.
According a recent article in The Wall Street Journal, "A quicker-than-expected recovery in U.S. manufacturing is resulting in supply disruptions and higher costs for materials used in everything from kitchen cabinets to washing machines to automobiles."
"The increased demand for these materials is showing up in manufacturers’ supply chains, which are clogged with orders, causing some producers to add weekend hours and overtime for employees. Orders that took a week or two to fill during the summer now require six to eight weeks, according to manufacturers coping with extended wait times for essential supplies."
While much of the unexpected upswing is based on consumers spending more, the entire global supply of components is being affected. This accounts for extended lead times and increased costs across many items, from fasteners to wire to raw materials.
The problems caused by increased demand for products is exacerbated by recent throttling down of staff at many manufacturers based on lackluster demand as the pandemic initially caused shutdowns or reduced capacity in many industries.
Add to that the shipping issues of the current period, and you have a perfect storm for supply chain issues from top to bottom.
Clearly, we are also still dealing with the Covid-19 pandemic itself.
From a recent article in Forbes, "The way to recover from this round of COVID-19 and future threats is to start building. From an economic perspective, supporting a robust manufacturing base is unbelievably important. If we look at the countries which have experienced impressive economic growth over the past 100 years, we’ll see that that growth was due to the development of a strong domestic manufacturing industry."
Long term, it seems that many countries are reaching for this goal - but it's not easy and it takes a long time to accomplish. The issues listed here will be with us for some time.
Some reasons this will continue in 2021:
- Capacities were reduced as demand plummeted during the initial phases of controlling the virus and early shutdowns.
- Quicker than expected recoveries in consumer spending is creating shortages of raw materials for all products and components, including industrial.
- Shipping globally is generally delayed and stacked up. Ships are frequently docked for days before being able to deliver loads. This further prevents emptied containers from returning to home for refilling.
- Costs have increased due to some tariffs increasing significantly.
- A general, global sense of nationalism is causing parts of the global supply chain to reshape, and change is never simple.
General products that are affected:
- Raw materials including aluminum, steel, wood and others.
- Computer components including many processors, RAM, SSDs, and many add-in cards because of chip issues.
- Fasteners and similar first-level components.
Some options for minimizing the negative effects:
- Consider placing orders now for products you know you'll need - that can give you an edge for total cost later in the year. This can also help absorb some of the shipping delays.
- If your products require components from international suppliers, consider stocking long lead time or custom parts to cover 2021/2022 demand.
- Budget for the increased costs and shipment delays now to prevent timeline shortfalls later.
The bottom line
Capital equipment manufacturers should also consider stocking programs for an assortment of subassemblies, with a special emphasis on long lead time components.
We realize that our OEM partners value our logistics management, and we plan to continue our vigilance through 2021 and beyond. It is critical that forecasts are updated and orders are placed as early as possible.
Sources:
Wall Street Journal, "Manufacturing Rebound Has Suppliers Struggling to Keep Up", January 2021
Forbes, "How to Solve our Supply Chain Problems", January 2021