5 Ways Flexible Outsourced Assembly Manufacturing Adds Value to High-Mix/Low to Mid-Volume Projects
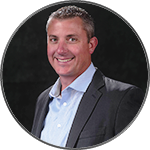
Written by Patrick Froh
OEMs producing high-mix, low-to-mid-volume products face unique challenges, from adapting to fluctuating demand to maintaining cost efficiency. Flexible manufacturing offers a strategic advantage, ensuring seamless transitions, reduced costs, and consistent quality. Below, we outline five ways flexible manufacturing delivers value, supported by specific examples of how GMI Solutions excels in these areas.
1. Streamlined Production Efficiency
One of the core challenges in high-mix, low-to-mid-volume projects is ensuring that production changes—such as switching between product configurations or even ramping up volumes—don’t result in significant downtime or resource wastage. Flexible manufacturing resolves this by enabling quick adjustments to equipment, workflows, and processes without affecting output quality.
- How GMI Delivers:
- Quick changeovers completed in hours, not days, ensure minimal disruption to production schedules.
- Modular workstations adapt to various assembly tasks, keeping production lines running smoothly even with complex product variations.
- Real-life example: GMI was building a low volume, high voltage cabinet for a medical OEM that was around 5 units/year. They then ramped to 20 and because of the size and complexity, GMI's operations and manufacturing team altered the build from a single work cell and broke down the build into subassemblies spreading out the work and ensure the utmost quality while ramping to the higher volumes.
This streamlined approach means faster project completion, better resource utilization, and fewer delays, which directly translates to cost savings and operational efficiency for OEMs.
2. Enhanced Demand Responsiveness
In industries where demand can shift unpredictably, the ability to scale production up or down is crucial. Flexible manufacturing allows OEMs to respond quickly to these shifts, avoiding costly overproduction or missed opportunities due to supply shortages.
- How GMI Delivers:
- Quick Response Manufacturing (QRM) production capabilities help reduce lead times and align production with real-time demand and has a built in buffer for capacity.
- Scalable processes enable seamless adjustments for urgent small-batch or high-volume runs.
- Real-life example: GMI was building a complex keyboard assembly for a medical OEM that required a fast ramp up where we went from 6,000/year to 20,000/year. Through DfM and other manufacturing efficiencies we were able to consistently meet their increasing demand while ensuring quality and on time deliveries.
This flexibility allows OEMs to remain competitive in fast-paced markets, making it easier to meet customer expectations without overextending resources.
3. Cost Optimization
For high-mix, low-to-mid-volume projects, controlling costs is always a top priority. Flexible manufacturing also means having a flexible yet reliable supply chain that drive costs down.
- How GMI Delivers:
- Streamlined procurement processes ensure cost-effective sourcing of materials.
- Having a supplier agnostic approach where utilizing relationships and suppliers that our OEMs have in place minimizes risk, quality concerns and provides continuous flow of materials.
- Real-life example: During a build transfer from internal to the OEM to GMI there were concerns on timeline and part quality risks. To alleviate these risks and keep on track of the timeline GMI assumed all of the current supply chain that was being used. Not a single supplier changed not even for screws and other hardware. Because of this we were able to transfer the build and start production in 90 days.
With flexible manufacturing, OEMs can achieve competitive pricing without sacrificing quality or delivery timelines, ensuring profitability even in challenging market conditions.
4. Quality Consistency Across Variations
Producing various products at lower volumes presents a unique challenge: maintaining consistent quality across every unit. Flexible manufacturing addresses this with rigorous testing protocols and highly standardized processes.
- How GMI Delivers:
- Lifelike or application level testing protocols are integrated into every build to ensure accuracy and precision.
- Electronic build instructions guide assembly and inspection processes, minimizing errors and ensuring repeatability.
- Real-life example: GMI built a robotic exoskeleton that needed rigorous testing and documentation. The final test was for a technician to put the suit on and walk the robotic system around the facility to ensure that the unit was working properly.
This attention to detail ensures that OEMs can trust every product that leaves the production line, safeguarding their reputation and customer satisfaction.
5. End-to-End Scalability
Flexible manufacturing addresses current production needs and positions OEMs for future growth. As product demand increases or new lines are introduced, scalable manufacturing solutions ensure seamless transitions without major disruptions.
- How GMI Delivers:
- Facilities are designed to support everything from prototyping to full-scale production, ensuring smooth scalability as projects grow.
- Adaptable workflows accommodate new product introductions without requiring significant reconfiguration or investment.
- Real-life example: GMI has a global footprint with redundant facilities that can support in region manufacturing for our OEM partners. With the ability to build in both facilities allow for scalability on a global scale where GMI USA was building an embedded computer for an OEM and needed to expand their volume to support Asia. GMI's redundancy and duplicate quality systems allowed us to seamlessly transfer the build to our Shanghai facility and increase the total output of the computers for our OEM to support their global growth.
This scalability gives OEMs the confidence to expand their offerings, knowing their manufacturing partner can grow alongside them.
Why GMI Solutions?
At GMI Solutions, flexibility is embedded in our high-mix, low-to-mid-volume manufacturing strategy. Here’s why OEMs consistently choose us:
- Flexible facilities: Modular workspaces and rapid changeovers ensure efficiency for any project size or type.
- Expert teams: Our highly trained operators excel in managing complex assembly tasks.
- Value-added services: Comprehensive supply chain management streamlines procurement and logistics through Seamless End-to-End Program Management.
- Focus on precision: Rigorous DfM practices and electronic build instructions maintain consistency and quality.